A fejlődés 2013-ban jutott el odáig, hogy elkészült az Urbee, az első autó, melynek teljes karosszériája és a szélvédői egy 3D nyomtatóból jöttek ki. Jim Kor futurisztikus, háromkerekű hibridje volt az első egyértelmű jele annak, hogy a technológia már jóval több lehetőséget rejt magában a modellezésnél. Ma pedig ez már hatványozottan igaz, annak köszönhetően, hogy már nem csak műanyaggal, de fémmel is tudunk 3D-ben nyomtatni.
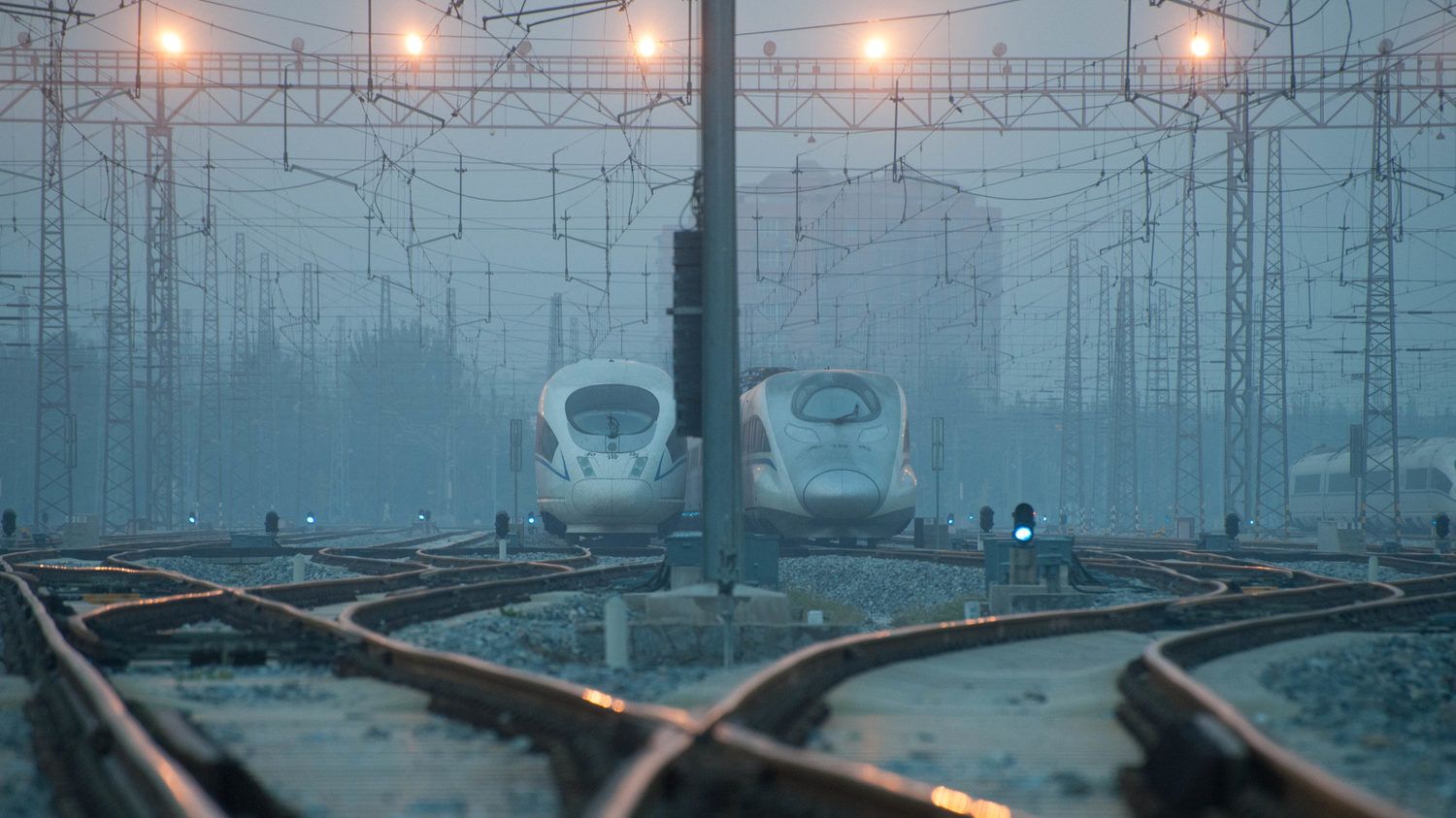
Évtizedekkel ezelőtt, a világ harmadik 3D nyomtatóját a Ford vásárolta meg. Tavaly decemberben a vállalat bejelentette, hogy egy 45 millió dolláros befektetéssel, 23 új 3D nyomtatót állítanak hadrendbe. Elsősorban pótalkatrészek gyártására használják majd őket, de a 2019-es Shelby Mustang GT500 fékrendszerében már megjelentek az első, végfelhasználásra tervezett, nyomtatott alkatrészek. Ahogy az olasz Bugatti is 3D nyomtatással készített titánium-féknyerget a világ egyik legdrágább szériaautójának számító Chironba.
A BMW szintén 2018-ban jelentette be, hogy a cég 3D nyomtatói túl vannak egymillió elkészített elemen, ami nem kis szám, különösen, ha figyelembe vesszük, hogy a német vállalatnál eddig csak a prototípusokhoz és fejlesztéshez használtak nyomtatott alkatrészeket, a kész autókban még nem.
De nyomtat már 3D-ben a Chrysler, a General Motors, a Honda, a Toyota, a Kia, a Mercedes és a Porsche is. Abban az iparágban, melyben a gyártók évente új modellekkel rukkolnak elő, iszonyú versenyhátrányba kerülnek azok, akik nem használják ki az új, adaptív technológia nyújtotta előnyöket, vagyis azt, hogy sokkal könnyebb, olcsóbb, gyorsabb legyártani vele egy alkatrészt, mint a hagyományos módszerekkel. Nem beszélve arról, hogy a 3D nyomtatás mekkora kreatív szabadságot biztosít a tervezőknek. Nem véletlen, hogy az ugyancsak 3D nyomtatókkal fejlesztő Volkswagen tervezési és fejlesztési részlegének feje, Martin Goede azt mondja:
Az ugyan még messze van, hogy egy teljes autó, minden alkatrészével együtt 3D nyomtatással készüljön el, de az biztos, hogy a közeljövőben robbanásszerűen emelkedni fog az ezzel az eljárással készített alkatrészek felhasználása."
Az autóipar mellett 3D nyomtatással készült alkatrészeket használnak többféle járműhöz is. Az Airbus A350-es utasszállító gépek néhány alkatrésze is már 3D nyomtatóval készült. A repülőgépek mellett a vasúti járművekre is tesztelnek ezzel a technológiával készült alkatrészeket. Az első 3D fémnyomtatót ipari környezetben Magyarországon a Knorr-Bremse Rail Systems Budapestnél helyezték üzembe. A gyártás prototípus előállítással kezdődött, nemrég pedig elindult a cégnél fémporból nyomtatott egyedi vonat fékalkatrészek tesztelése, és a validálási folyamat előkészítése.
Az ezzel a technológiával készült alkatrészek kisebbek és könnyebbek, mint elődeik. Ez a gazdaságos alapanyag felhasználáson túl azért is fontos, mert a modernebb vasúti kocsik a kényelmi szempontok miatt nagyobb utastérrel rendelkeznek, alacsonypadlósak, ezért a biztonságtechnikai rendszereknek kevesebb hely jut. A 3D technológiával nyomtatott fékalkatrészek a térfogat és súlycsökkenés ellenére ugyanolyan biztonságosak, mivel megőrzik a hagyományos eljárással készült alkatrészek mechanikai tulajdonságait.
A járműipar jövőjét, beleértve a vasúti-és légi közlekedést, egészen biztosan a 3D nyomtatás jelenleg zajló forradalma határozza meg. Felgyorsítja a fejlesztést, a tervezésben új formákat és megoldásokat hoz magával, a járműveket pedig könnyebbé teszi, így csökkentve az üzemanyag-fogyasztást és gyakorlatilag megszünteti a pótalkatrész-hiány problémáját. Mivel a fejlődési folyamat elején járunk, mindez csupán kezdet, a távlatok egyelőre beláthatatlanok.